EXPERTISE
Standard Operating Procedures for Medical Devices — Project Management Must-Haves
Medical Device Standard Operating Procedures (SOPs)
The cornerstone of successful Quality Management Systems (QMS) are deliberately prepared standard operating procedures (SOPs). Standard operating procedures for medical devices outline recurring operations or processes and help to maintain quality and consistency. To remain compliant with regulatory agencies including the Federal Drug Administration (FDA) and International Organization for Standardization (ISO), medical device companies need to develop SOPs that outline a variety of operations, such as those for manufacturing, risk management, and training.
If you need assistance determining when and how to establish SOPs for your medical device company, contact QA Consulting today to get started.
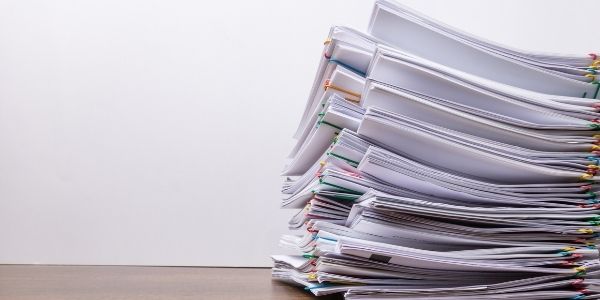
When To Establish An SOP
Ideally, you’ll generate SOPs early on in product and company development. Why? As your company and team grows, SOPs are required to ensure procedures continue to be executed properly and consistently. They provide quality and reproducibility, creating a foundation for success.
For medical devices, this translates to optimal safety and effectiveness. In addition to the benefits of quality SOP design to your company, medical device companies must generate SOPs to remain compliant with regulatory agencies.
In the United States, medical device companies must comply with the FDA quality system regulations (QSR) outlined in 21 CFR Part 820. The FDA QSR requires medical device companies to develop and maintain medical device SOPs that describe and define the “manner of production.” These include the development and maintenance of standard operating procedures for medical devices pertaining to all aspects of your workflow:
Whether manual or eQMS, QA Consulting can help. We can assist in your selection and implementation of an appropriate eQMS or set up a manual system and establish a purpose-built medical device document control system for you.
- Medical device design
- Medical device development
- Complaints management and resolution
- Internal and external training and policies
- Management review
- Manufacturing and production operations
- Equipment maintenance
- Environmental controls
- Contamination prevention
- Obtaining and disposing of materials
- Building maintenance
- Data management
QA Consulting is experienced in SOP development and implementation for medical devices. As we develop SOPs, we leverage our regulatory, quality, and microbiology know-how to ensure your company is compliant and audit-ready, regardless of the market.
Key SOP Content
- Purpose and scope. Why is this SOP being developed? What operation(s) or procedure(s) are described?
- Roles and responsibilities. Who is responsible for executing the described operation or procedures? Who is responsible for verifying and maintaining the SOP?
- Background. This section provides the necessary background information to contextualize the SOP and provide any critical information that a new user or auditor may need to know.
- Procedure steps. This is where the actual step by step directions for each operation or procedure is outlined. An introduction summary or schematic overview of these steps may be included.
- Glossary/Definitions. Define critical terms that are used in the SOP.
- References. A list of the reference documents used to generate the SOP.
- Supporting material. Any supplementary resources relevant to the SOP.
- Document and revision records. A record of all changes made to this SOP, when they were made, and who made them.
The FDA provides medical device SOP examples. You can find other medical device SOP templates online, but medical device companies — especially smaller companies — should be wary of using these templates rather than consulting an expert to create a custom SOP solution. These medical device SOP examples are typically created with large companies in mind and may not be relevant or useful for smaller companies or startups. Regardless of size, all medical device companies will benefit from a custom SOP design solution that meets the specific needs and regulations for each device and company.
Let QA Consulting create a custom solution for your medical device company today.
How To Maintain An SOP
- Processes and operations change
- Roles evolve
- They modify their trainings
- They update information and resources
- New or updated products are introduced
Medical device companies should create a schedule to review all SOPs annually. The review schedule and the role(s) of the reviewer(s) should be outlined in the SOP.
Outsourcing QMS Project Management and SOP Design
- Improve the success of in-market products
- Streamline employee training
- Shorten the time to market for new products
- Produce consistent results
- Identify risks and produce risk management strategies
- Decrease the risk of audit nonconformities
- Ensure your company remains in compliance at all stages
Still unsure if outsourcing is your best path forward? Check out our article on exactly what type of companies should look externally for help.
QMS Project Management and SOP Design with QA Consulting
QA Consulting project managers have the experience and expertise to meet the QMS project management needs of your medical device company, regardless of the size or scope of your company.
Our project managers will approach your SOP generation by dividing the SOPs across multiple phases in an order that best fits your company’s workflow and development process.
With each phase, they will:
Conduct an up-front phase consultation
To kick off each phase of SOPs, your project manager will meet with you to introduce the planned procedures, brief you on their general requirements, and discuss how your company will be able to fulfill those requirements.
Author your SOPs
The project manager will use the feedback learned from the phase consultation to begin authoring your procedures, adapting and incorporating best practices as well as your company’s unique requirements into the regulatory requirements for each SOP.
Train on implementation
Once all SOPs in a phase have your approval, your project manager will collaborate with you in a session dedicated to training on the SOPs and discussing best practices for implementation.
Are you looking for an expert to help establish SOPs that help you maintain quality and compliance throughout your medical device workflow? Connect with QA Consulting’s project managers!