Tap into our expertise. Our network. Our strategies.
The process of medical device design, production, verification, and validation is iterative, informed by stepwise review throughout. QA Consulting has extensive experience in the stages of medical device development that bring best practices of design verification and validation to your facility.
QA Consulting can help generate and execute a comprehensive, tailored strategy for you. Here are our core areas of expertise in design verification and validation:
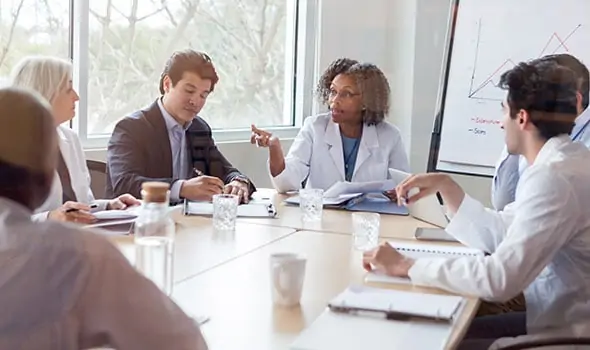
An Optimally-Designed Partnership with QA Consulting
Medical device design verification and validation regulations continue to evolve. When you partner with QA Consulting, you get an expert with networks and up-to-date knowledge of all regulatory requirements to yield efficient design verification and validation processes.
The benefits:
- Stay compliant with all applicable regulations
- Execute design verification testing and design validation using our existing network of testing facilities and qualified healthcare providers
- Leverage the established systems at QA Consulting for more rapid deployment of device production
- Avoid common mistakes and pitfalls, saving time and money
We are eager to share our knowledge. You can find some expert insights here, or reach out to our team to get your challenges solved.
Design Verification vs. Design Validation
Medical device verification and validation are each critical, but what is the difference?
While verification ensures that a medical device is produced and operates as specified, validation ensures that the medical device delivers the intended medical benefit or use.
Design Verification:
- Confirms the device meets the input specifications
- Ensures the medical device design specifications are accurately achieved
- Usually conducted via inspections, tests, and analyses of the final device product
- You can outsource medical device verification to an ISO 17025-certified lab
Design Validation:
- Confirms the medical device meets user needs and can be used as intended.
- Conducted by a qualified individual, such as a healthcare professional, to confirm that the device meets its intended use
- Not to be confused with process validation—a completely different topic that you can learn about here.
Keep this in mind: manufacturers must conduct medical device design verification and design validation on the final medical device, not during prototype development or preliminary research.
Human Factors and Medical Device Design
Medical device design should consider the end user, their behaviors, the conditions in which they will be using the device, and their knowledge of the device.
Misuse of medical devices can impair the ability of healthcare providers to deliver quality care, and in some cases be catastrophic to patient health. Because of this, the FDA has issued guidance to medical device companies on incorporating human factors into the design process.
Expert Tip: modifications to user interfaces — all points of interaction between the device and user(s) — are the most effective way to minimize user errors and use-related hazards.
Though human factors are considered during design, evaluating how well these considerations minimize use errors and hazards requires empirical testing. At the end of the development process, manufacturers should perform human factors validation testing to assess user interactions with the device in real-world settings.
QA Consulting is an expert in integrating the human condition into medical device design. If you need assistance incorporating human factors into your medical device design or performing human factors validation testing, contact our team!
Design Controls
Medical device design validation is a component of design controls that (in part) demonstrates the safety and efficacy of the medical devices to meet User Requirements. Design controls are part of a larger quality system, and were introduced into the FDA’s Quality System Regulation (QSR) in 1996 and implemented in 1997.
Per 21 CFR Part §820.30, medical device companies “shall establish and maintain procedures to control the design of the device in order to ensure that specified design requirements are met.”
Though design controls are defined by the FDA, similar assurances are required by regulatory bodies in Europe, Canada, and elsewhere — though differences exist among these requirements.
When should you establish design controls?
Manufacturers should establish design controls when they have the intent to produce a medical device.
A key component of design control is traceability, specifically outlining how each stage in the design process (e.g., user needs, design input, design process, design output, and final product) relates to and informs one another.
QA Consulting is an expert in helping medical device manufacturers establish design controls. Through our years of experience, we’ve identified common pitfalls and ways to overcome them.
Design Transfer
Design transfer is exactly that: transfer of all the design specifications and other elements necessary to commence medical device production — the handoff between the development and production teams.
Your company has spent time and effort developing a design that meets user needs, considers user factors, and minimizes use-associated risks and errors. Along with design controls that ensure safe device production, it’s important to consider how all of these specifications transfer to production teams.
In addition to the transfer of design specifications and controls, design transfer also includes ensuring other production components are ready to go. Are all materials, equipment, and people in place to begin production?
Poor design transfer can result in inconsistent production, costly errors or delays, or impacts to the safety and efficacy of the final product.
To avoid these issues, some best practices for seamless design transfer include:
- Start early. Prepare for transfer during the design process.
- Have design transfer procedures in your design controls.
- Utilize the expertise of the manufacturing team and design transfer experts.
- Don’t reinvent the wheel. Use established advice and checklists (like this one from QA Consulting).
Need assistance managing design transfer?
Medical Device Design Verification and Validation with QA Consulting
QA Consulting is ISO 13485 certified and experienced in the United States and international markets. At QA Consulting, we ensure that clients are equipped with the expertise to become competent in regulatory and quality affairs for their medical device verification and validation needs. We work as an extension of our clients teams, developing customized solutions to meet your goals and needs and working together to ensure your success.