Author: Anne Holland, CEO and Founder
Verification and validation are crucial aspects of a medical device’s development. They work together to comply with regulations, ensure a high-quality device, and prove safety and efficacy for the end-user. But what’s the difference between the two?
Verification and validation are different processes with different goals that are often mixed up.
While there are multiple areas of the device lifecycle where verification and validation play a key role, below you will find an overview of design verification and design validation.
What Is Design Verification?
Medical device design verification is the process of testing to specification. It’s a technical process that verifies that your product does everything you claim it can do. For all devices and design controls, you should have clear, measurable specifications, called design inputs. Then, you take representative units of your final device, test them, and compare those results to ensure they meet the predetermined acceptance criteria.
An important note: these units must be representative and not a prototype.
For example, if your surgical instrument is supposed to be 12 inches long, you should produce an instrument that’s representative of your final product, measure it, and ensure it is the correct length. The same process applies to an instrument that is designed to meet a specific torque specification. To verify this, you would run a test on a statistically valid sample size that applies rotational force and ensure that it can handle that torque level.
It’s a common practice to outsource verification testing to an ISO 17025 certified lab. These labs manage their tools and equipment in accordance with international standards, ensuring your verification results are legitimate.
However, you should not solely rely on the lab for testing protocols. Medical device manufacturers should:
- Generate internal protocols
- Review them with the test facility
- Agree upon them before verification testing occurs
Test results should then be added to your internal test report for further analysis.
What Is Design Validation?
While verification focuses on verifying device specifications, medical device design validation ensures user needs and intended uses are met. Instead of verifying a specific part of the device’s design is correct, validation tests the device as a whole, with particular attention paid to the user’s interactions with the device.
During the design validation process, user requirements drive the design inputs. It’s typical to use layman’s terms such as: “a torque wrench has to be on the end of the instrument” or “the instrument needs to be long enough to meet a user’s spine.”
To validate this, you would engage a qualified outside source such as a surgeon and have them evaluate your product to ensure it meets its intended use. They may validate that yes, you have met the intended user requirement, or no, you have not.
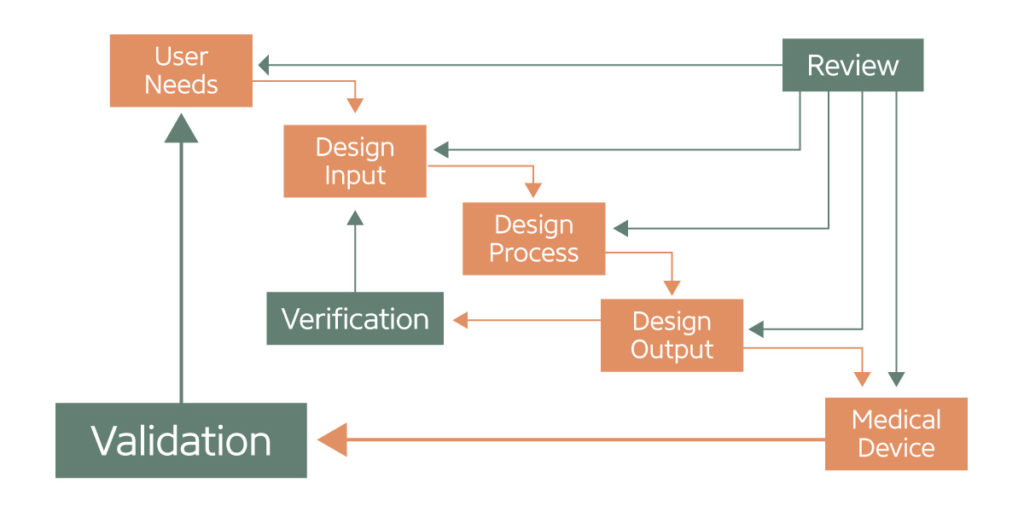
Application of Design Controls to Waterfall Design Process. (Figure adapted from FDA Design Control Guidance for Medical Device Manufacturers.)
Common Verification and Validation Roadblocks to Avoid
Verifying and validating the design of your product is an essential part of getting your product to market.
That’s why it’s in your best interest to avoid making these mistakes:
- Not using representative units. You must manufacture the product you’re verifying or validating as though it’s your final commercially available device.
- Cutting corners to save money. Some verification and validation tests may be expensive. However, they’re necessary, and cutting corners at this phase may result in unexpected costs down the road.
- Rushing the design verification and validation process. If you don’t verify and validate your product correctly, ultimately, it will delay your time to market.
- Receiving validation from someone who is not qualified to do so. Individuals involved in the design or development of a device may not validate it. It must be a typical user, not someone with background knowledge of the device.
Lean Into Our Verification and Validation Experience
Making design verification and validation mistakes often ends in unfavorable outcomes such as product approval delays. Enlisting the help of medical device quality consulting experts to ensure the entire process goes smoothly leads to faster time to market and fewer roadblocks along the way.
QA Consulting’s vast experience in medical device risk management and, more specifically, the design verification and validation process helps us guide our clients towards their end goal—a device that’s compliant, high-quality, and effective for users.
Let’s get the quality conversation started.
Medical device manufacturers may also reference the FDA’s Design Control Guidance for FDA 21 CFR 820.30 and Sub-clause 4.4 of ISO 9001 for further details.