Team Member Spotlight: Kathy Johnson
Broad Expertise. Collaborative Culture. Individual and Tailored Approach.
At QA Consulting, we work as an extension of our client’s in-house team, so building a close working relationship from the start is essential for project success. We support rapport-building by regularly spotlighting our team members so you get to know the people behind QA Consulting. Meet Kathy Johnson, Human Factors and Usability Engineering Consultant.
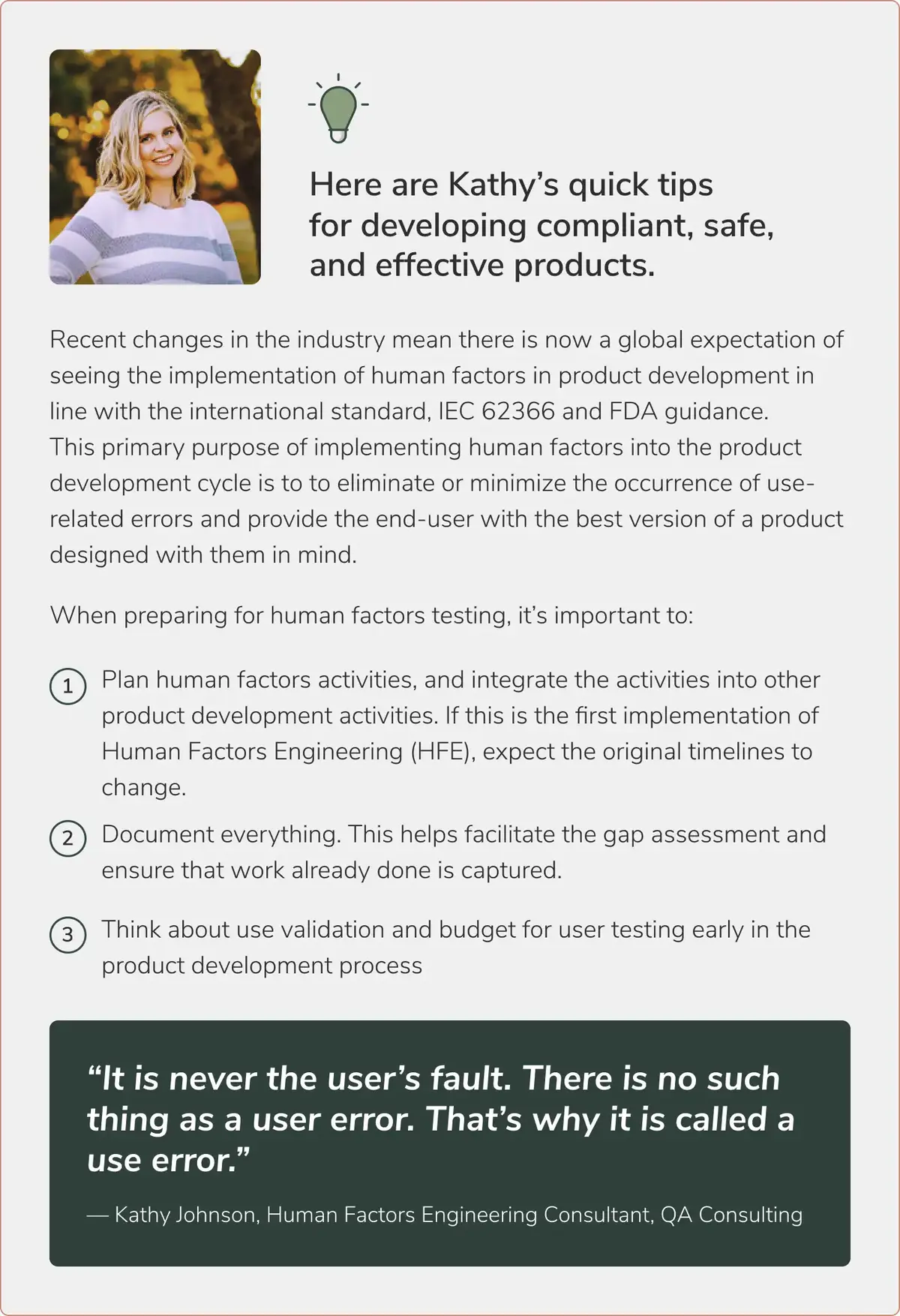
Get to Know the Experts — Five Questions with Kathy
1. What is human factors engineering, and how has the need changed in the industry?
Human factors engineering is about integrating the human condition into your medical device. It focuses on the user and use environment, ultimately resulting in a safer, better, more effective product focused on the user.
Human factors and usability engineering have been around for years but not enforced. So while the business benefits, such as the reduction of development time and money saving, still stand, there’s now growing pressure from the FDA and other regulatory bodies to consider the medical device’s user touchpoints and adopt a use-related risk approach.
Human factors engineering is now a requirement. When you submit, the FDA and other notified bodies will look for the human factors data. Because of this, human factors needs to be considered earlier in development, ideally during feasibility when work begins on understanding the user profiles and use environments.
2. How did you get into human factors engineering?
I went to grad school and got a master’s in biomedical engineering, and during grad school, I realized I did not want to work in a lab, that it was not for me. So when I went and got my first job, it was in medical devices as a technical trainer. I loved teaching people; at some point in my life, I wanted to be a teacher, and I thought, well, this is a perfect balance—I get to work within science and biology and teach people about these innovative and cool products. Then I moved into the IVD or in vitro diagnostics industry and continued training there.
I got to experience and see what users thought of the products as you taught them how to use the product. There would be many questions about why the product was made a certain way or why the software behaved the way it did. And I really didn’t know the answers. At some point, the marketing or product development teams made these decisions. I thought it was interesting. In 2015, I was given an opportunity to start a human factors engineering group, so I did.
3. What first attracted you to QA Consulting?
After some time, I decided to leave the industry and went into independent consulting because I wanted more time with my kids. Independent consulting is great for lots of things. You make your own schedule and get to pick and choose who you want to work with. But what you don’t have is resources at your fingertips.
What I love about QA Consulting is 1) it is close to home, 2) it has an excellent reputation, and 3) it holds an abundance of resources you could reach out to and tap into at any time.
I don’t have expertise in some things. No one does. But it’s good to know someone’s an email or phone call away. It’s nice to have a helpline on the side. With so many areas of expertise covered, if we need an answer, we can get one.
4. What can medical device companies expect when working with you?
From the project kick-off, my priority is really ensuring the medical device company I am working with understands usability. I tailor my work to each client’s independent needs, so the first thing I will do is look at their documentation and perform an initial gap assessment. This is because they might have already done some of the human factors work without realizing it was human factors engineering. This way, we streamline our approach and ensure we are not re-covering old ground. So part of my role is still in teaching—helping to cultivate an understanding of human factors engineering and realistic timeline expectations, clearly and early.
One thing a lot of my clients need help with is the realization that regulatory bodies expect the manufacturer to implement human factors testing to minimize use errors. I remind them that a good medical device is designed for the user and that incorporating human factors much earlier in the manufacturing process creates the necessary budgets and timelines to do this properly. This forward-thinking enables medical device companies to make the required design changes often and early—keeping costs and unexpected delays to a minimum. So it is better for everyone.
5. What’s one thing we’d be surprised to know about you?
Well, I am originally from New Jersey. But I have been living in Texas for 17 years now. I moved down here for grad school and loved it. I never want to leave, and somehow I convinced my entire family to move here too, so all my direct family and some extended family are here. We’re working on a couple of others too. So we’re working on a migration from New Jersey to Texas.
What Kathy is Reading
- IEC 62366-1 — Application of usability engineering to medical devices & the accompanying technical report IEC 62366-2
- FDA Guidance — Applying Human Factors and Usability Engineering to Medical Devices
- FDA Draft Guidance — Content of Human Factors Information in Medical Device Marketing Submissions
- ANSI/AAMI HE75:2009 (R2018) — Human Factors Engineering: Design Of Medical Devices
Also, don’t miss what’s new on our blog: https://qaconsultinginc.com/blog/
Develop safer products with human factors engineering you can rely on.
Contact us today to set up a discovery call!